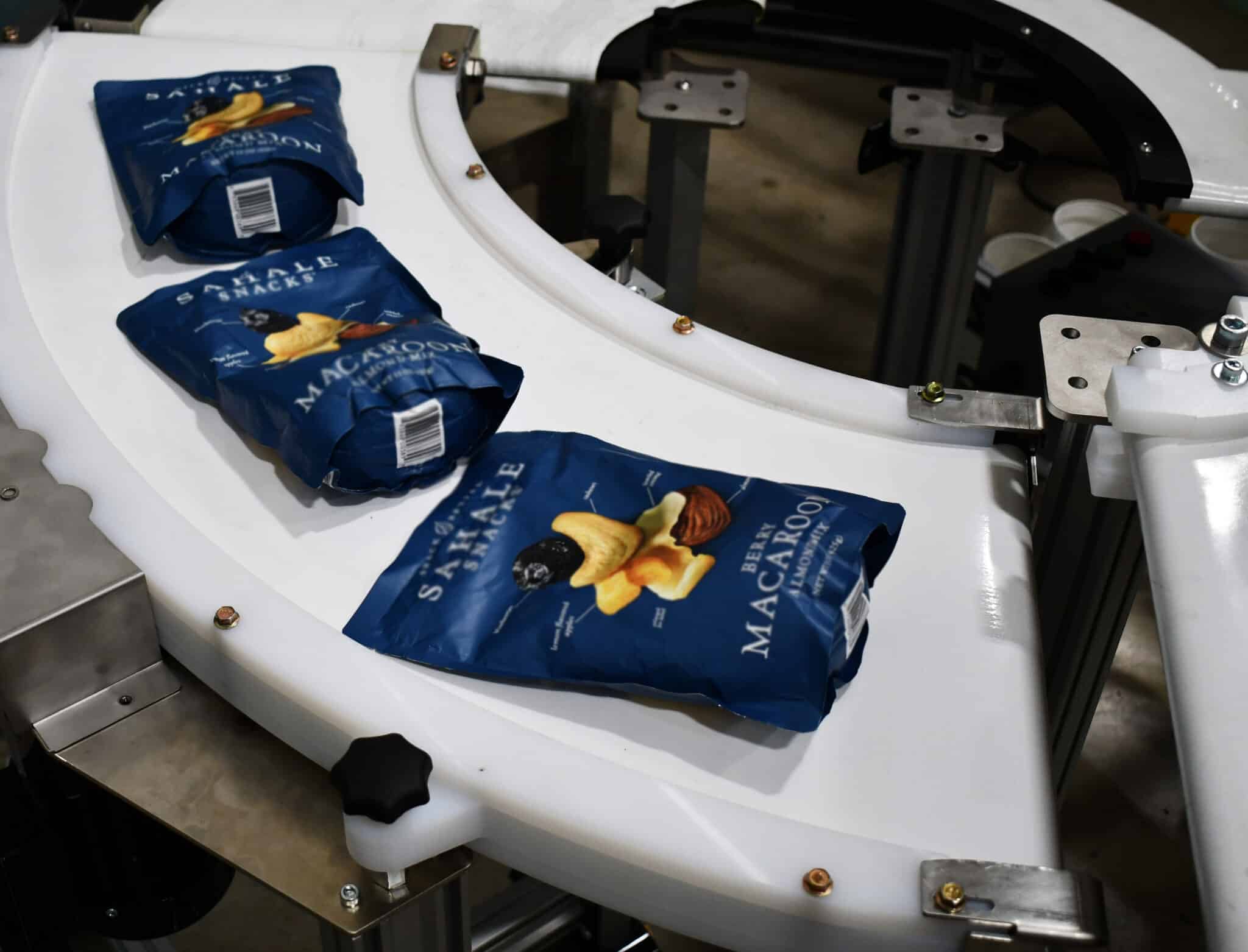
The C3 Compact Curve Conveyor is a game-changing solution designed to optimize packaging processes across the packaged food industry. By improving efficiency and adeptly managing a variety of product sizes, it caters to manufacturers facing spatial constraints within their facilities.
The Challenge
In many snack food operations, a rising demand for packaged products has led to notable bottlenecks along the packaging lines. Traditional linear conveyor systems often necessitate excessive manual handling, particularly at curves, which not only diminishes throughput but also escalates labor costs. Additionally, limited floor space often hampers efforts to expand conveyor systems, resulting in operational inefficiencies.
The Consultation
Dorner’s engineering team conducts an initial consultation to better understand their specific packaging requirements and operational challenges. Key pain points that are identified included:
Floor Plan
Inefficient conveyor layouts can restrict product movement, notably at corners, due to their linear configurations. Space optimization is crucial for facilitating streamlined workflows.
Manual Handling
High levels of manual intervention can increase labor costs and heighten the risk of product damage. The industry increasingly needs automated solutions to minimize human reliance and enhance operational efficiency while also mitigating pinch points that can lead to product damage.
Product Flow
Maintaining a smooth and secure transfer of products between packaging stations is vital for preserving product quality and minimizing disruptions. Ensuring products exit each stage of the production cycle in the correct orientation is essential for operational success.
The Solution
Dorner’s engineering team has developed the C3 Compact Curve Conveyor as a targeted solution to address these industry challenges:
Floor Plan
The C3 features customizable curves—available in 45°, 90°, and 180°—that enable efficient redirection of products, thereby optimizing the use of available production space. This flexibility allows manufacturers to adapt their conveyor layouts to accommodate both current and future production needs.
Reduced Manual Handling
By automating the conveying process, the C3 significantly lowers the requirement for manual handling. This advancement not only alleviates employee workloads but also results in reduced labor costs, thanks to improved throughput. Its 25mm nose bar facilitates seamless integration with existing automation systems, enhancing overall operational flow.
Enhanced Product Flow
The C3 is adept at managing a variety of product sizes and shapes, ensuring smooth transitions between different packaging stations. This capability minimizes the risk of product damage while improving overall quality. Additionally, it preserves the leading edge of products as they’re transferred to subsequent operations.
Space Optimization
With its compact design, the C3 offers better spatial utilization, enabling facilities to maximize their existing space. This allows manufacturers to create additional packaging stations, increasing production capacity without the need for extensive renovations.
The implementation of the C3 Compact Curve Conveyor represents a significant advancement in achieving enhanced efficiency and scalability within the packaged food industry. This solution empowers manufacturers to meet growing market demands while upholding superior quality standards in packaging. As a result, there is potential for further exploration of automation initiatives to elevate productivity levels even more.